銅メッキ加工で旧車BМWのエンジンカバー
2019年08月15日
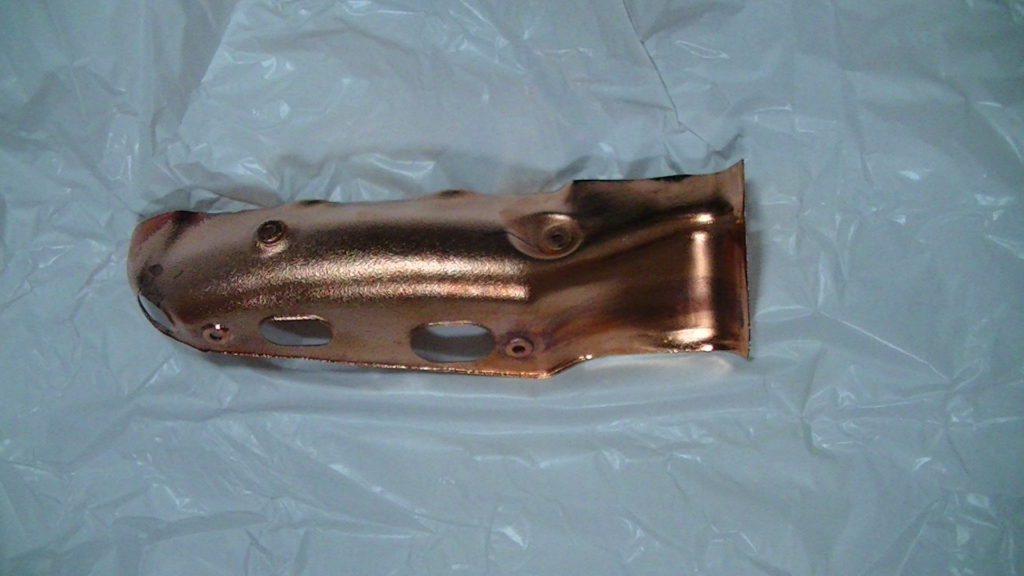
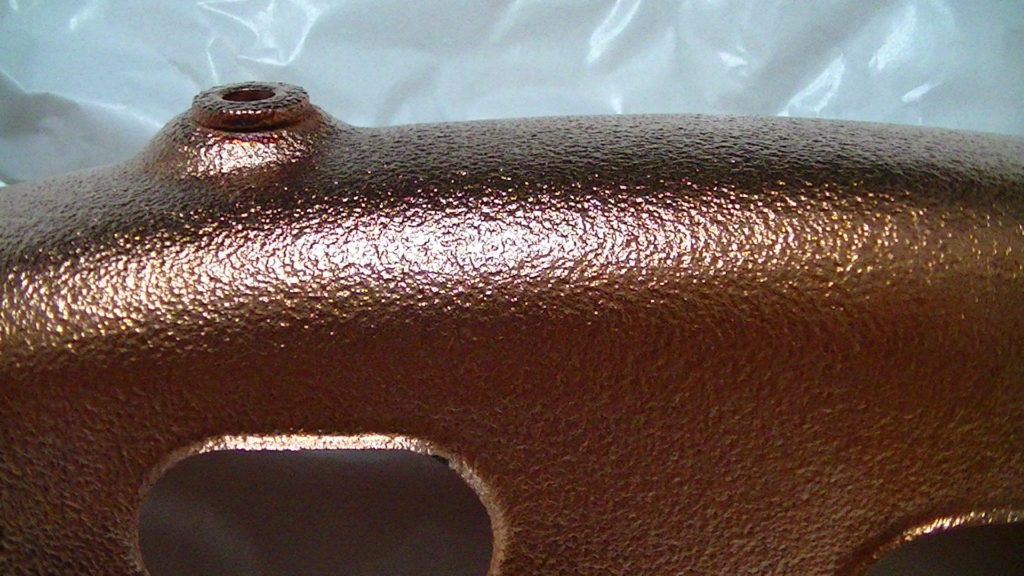
このパーツは、旧車BМWのエンジンカバーです。素材はスチール製でボルト留めする穴が数か所あるのですがその箇所には同じスチールの金具をろう付けしています。このオーナー様は個人様で初めてのお取引で弊社の工場に持ち込みで来られました。検品させて頂いた時にブラスト痕(ショット)がエンジンカバー全体に見えていました。元々このパーツの表面には塗料が付いていて表面が錆でザラザラな状態であったのでお客様は剥離剤に浸すと錆も溶けて貫通穴が出るのを恐れてブラストで塗料を落としたとおっしゃっていました。オーナー様はクロムメッキ加工をご希望されておらず、再度オリジナル塗装を施す下地として塩化銅メッキを分厚くして腐食しにくくする為の作業依頼でした。ですので少し色合いが違うかも分かりませんが、これも銅メッキ加工なのです。通常の銅メッキ加工よりも分厚くしている為に銅メッキ槽に時間を長く漬け込んでいます。当然、この上に塗料で覆い隠す為にバフ研磨作業も省いております。加工としては脱脂作業及び塩化銅の長漬けと言う工程です。これで腐食しにくくなります。今回のご依頼の目的は滅多に御座いませんので皆様にご紹介をさせて頂きました。他にも腐食しにくいメッキ加工としまして溶融亜鉛メッキやユニクロメッキそしてクロメート等が御座います。今回のお客様の様に様々な用途にメッキを用います。基本的に金属類の多くの素材は素材に腐食しにくい物で覆い隠さなければ錆が出てきます。その為にメッキが有ります。弊社で特化しているクロムメッキ加工も腐食を防止するメッキの1つですがその付加価値として銀の様な綺麗な光沢を出す加工もある訳です。メッキ加工の種類は数100種類あります。なかなか全てのメッキの長所と短所を覚えてお客様がご判断される事はまず不可能です。弊社は全てのメッキ加工に精通しております。お客様のご依頼したいパーツをどの様な用途で使用する事をお考えなのか?そのお考えを教えて下されば最適なメッキの種類をご提案させて頂いた上で、弊社でメッキ加工を施させて頂きます。因みに樹脂部品に於いても同様です。樹脂は金属類よりも腐食しにくいですが経年劣化によって段々と素材が硬くなりしまいにはヒビが表面に入り割れてしまいます。そうならない様に樹脂表面にもトップコートやメッキを用いて保護いたします。
カテゴリ:ブログ