スズキカタナ400と1100のステッププレート、シートブラケットにメッキ加工
2019年07月17日
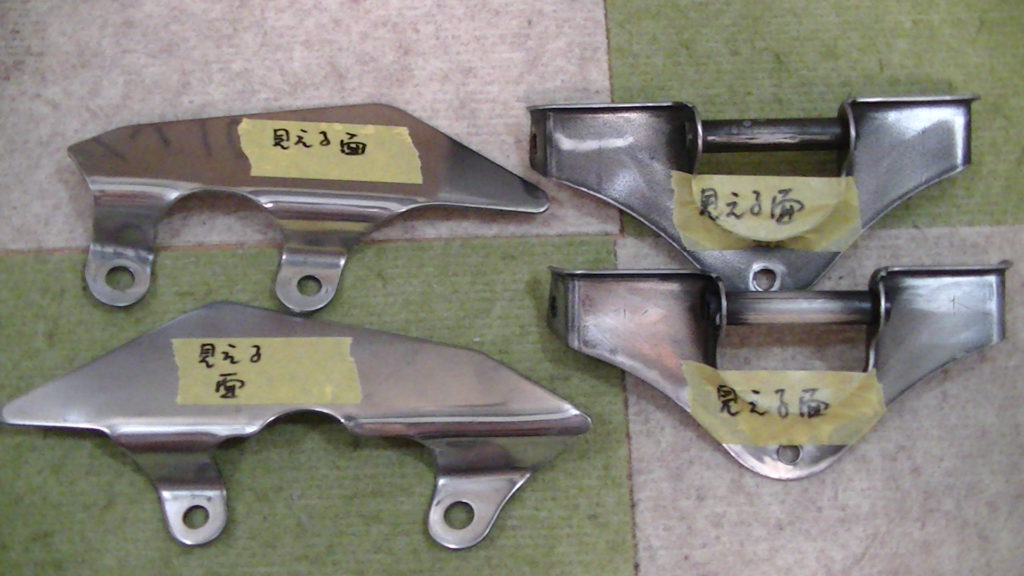
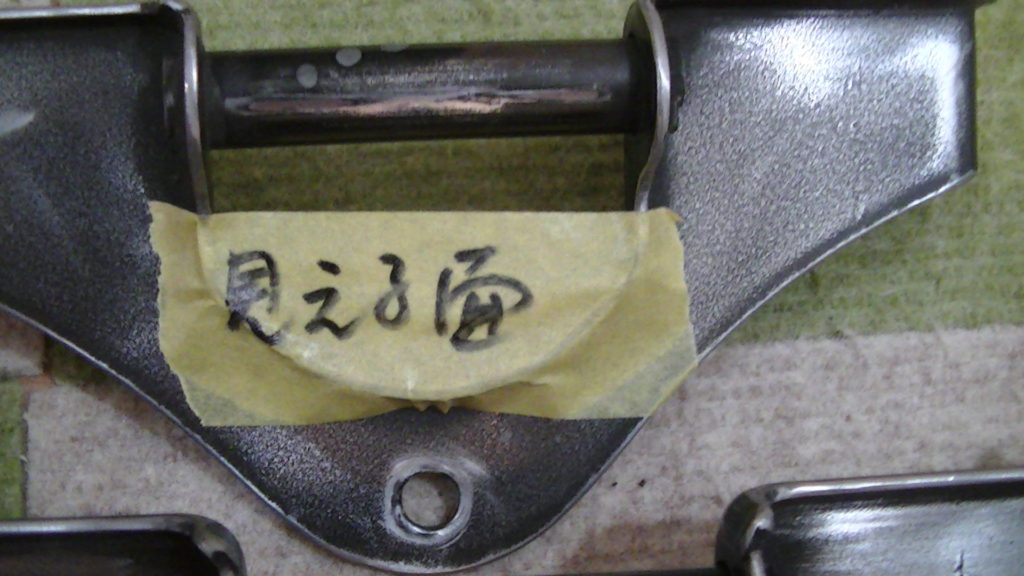
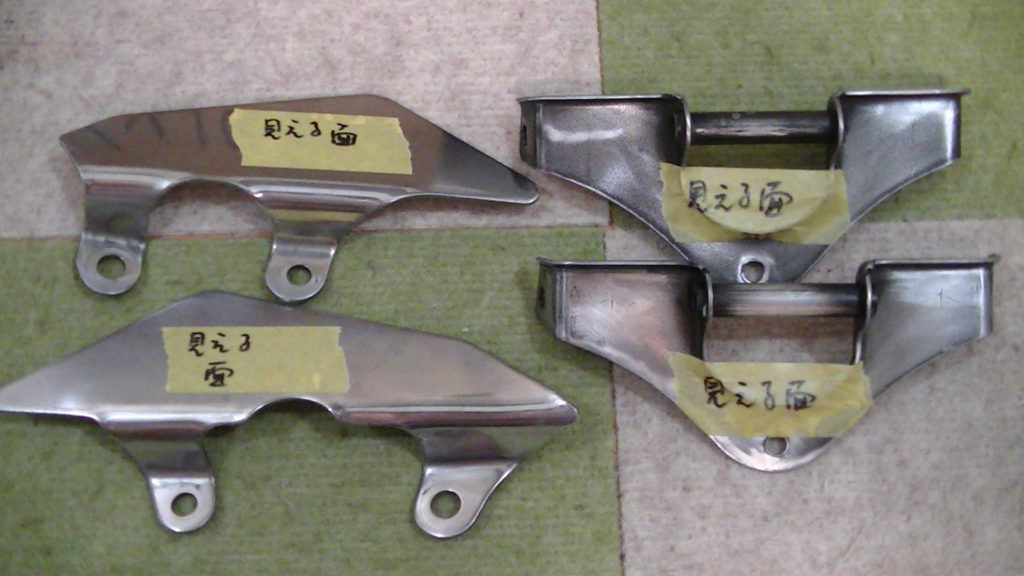
上の写真は、ステッププレート左右1994年式スズキのカタナ400の純正部品です。もう1つは1990年式カタナ1100のステッププレートシート受け前のブラケットです。素材は全パーツスチールです。スズキのカタナは1980年代頃から初代が誕生して現在も世界的に人気のバイクです。(一時期生産中止されていました。)両パーツ共にクロムメッキ加工を施してバイクに装着すると大変綺麗に見えます。今回のお客様は業者様で綺麗にしたい箇所に分かりやすく見える側と印を付けて頂いています。ボディ側は見える事が無く、加工賃もお安く済むのをお分かりになられてこの様に印を付けてくれました。剥離は部品の前面になりますが、バフ研磨作業は両面より片面の方が当然手間が半分になる事からお安くなります。もしこのブログをご覧になって弊社にメッキ加工を出されるお客様や業者様はご覧の様に印を付けて頂いてご発送される事をお勧め致します。業者様のご指定で今回は厚メッキ加工(中ランク)で加工をお受けさせて頂きました。それでは加工方法をご紹介させて頂きます。全4パーツ共に剥離致します。素材的にはカタナ400のステッププレートよりもご覧の様に1990年式のカタナ1100の素材が悪いです。元々新品でも素材の表面が悪かったのかも分かりませんが・・・・目を凝らして見てみるとスチール表面にザラザラした様な物が見え、又、加工する上での傷の様な物も確認できます。ブラケットの形状はバフが当たり難いので上メッキ加工を選択したとしてもツルっとした面にはならない事が想定されます。この様な時にはクロムの下地の銅を3度漬けすると幾分ましになる事が御座います。もう一つは鏡面ポリッシュ用ルーターで磨きこむと言う方法も御座います。しかしその様な場合は追加料金が発生致します。これらの見栄えのクオリティは各お客様のお考えによりますので弊社はお客様のご希望通りで仕上げさせて頂いております。弊社の厚メッキ加工(中ランク)で大手トラックメーカー様の純正クロムメッキバンパーと同じメッキ厚になります。この様なバイクパーツで有るならば中メッキ加工で十分な仕上がりになります。皆様も大手自動車メーカー様の純正メッキ部品を起点にお考え頂くと商談がしやすくなります。話を戻しましてバフ研磨後は銅メッキ加工を行って2度目のバフ研磨でピンホールを埋めます。そして2回目の銅メッキ加工を行いニッケルメッキ加工、そしてクロムメッキ加工を施します。
カテゴリ:ブログ