昭和42年式日産フェアレディ―SR311の三角窓を板金加工及び再メッキ加工を施す
2019年05月15日
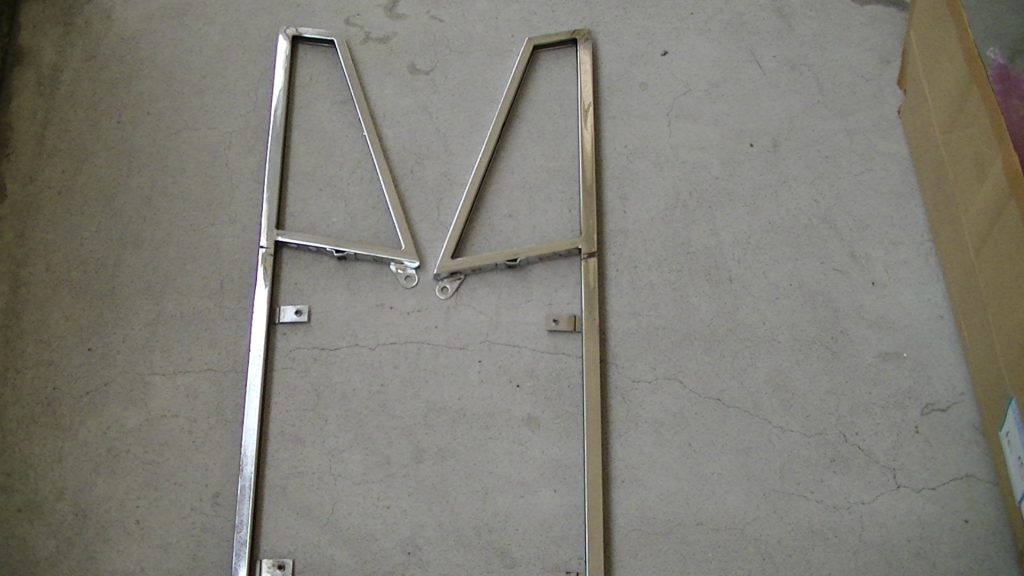
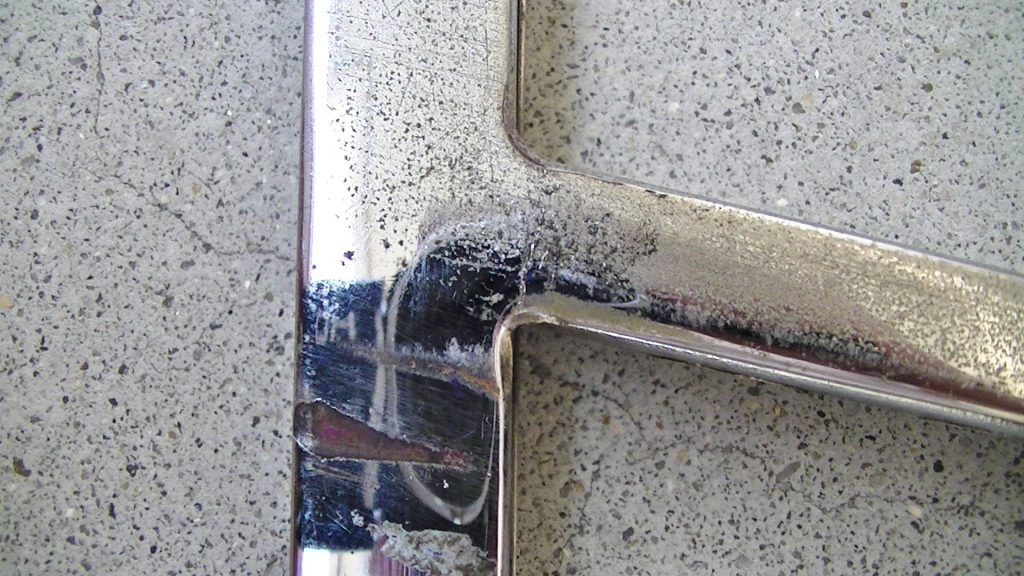
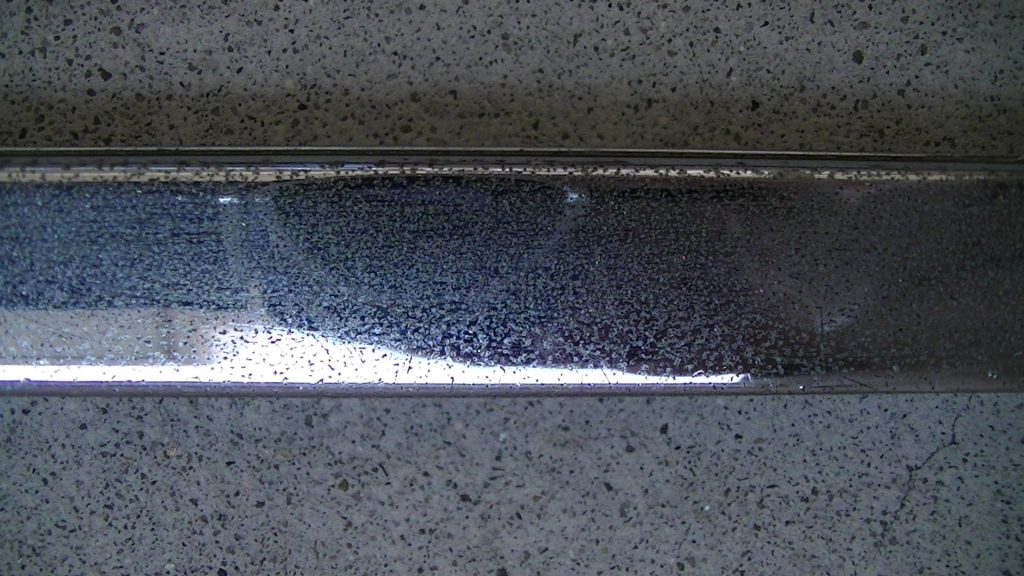
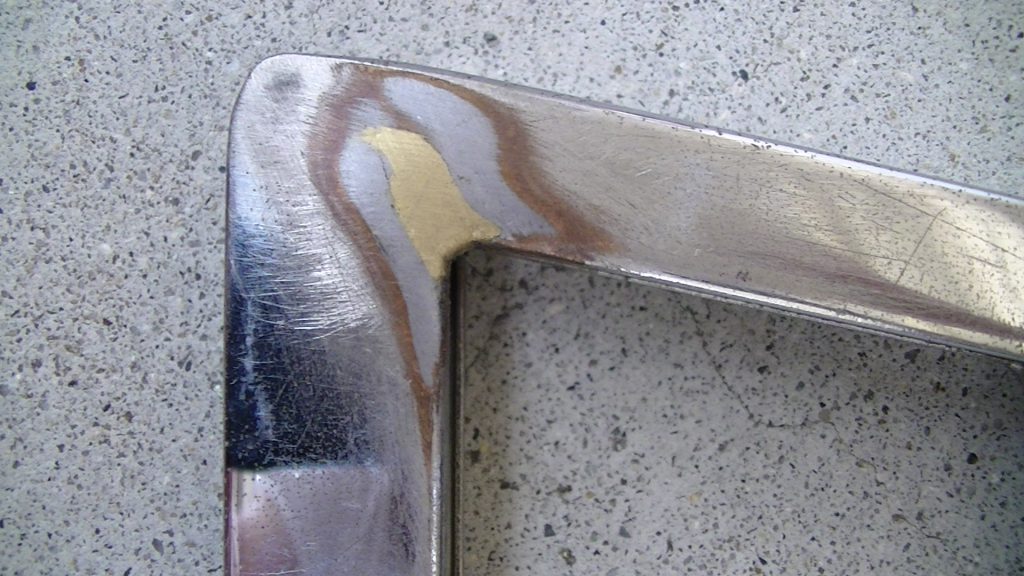
この写真の三角窓はスチール製で昭和42年式(52年前)の日産フェアレディ―SR311に装着されているパーツです。ご覧の様に全体的に腐食痕が目立ち尚且つアップ写真の様にお客様ご本人でろう漬け板金されている状態で再メッキ加工をご希望されています。因みに、このフェアレディSR311は希少価値車で2000ccの排気量4気筒ソレックスキャブレターを2基、当時としては最先端のU20型エンジン(145馬力/6000rPm)でした。国産初の200キロ/時オーバーで話題になった自動車です。今でこそ2000ccで145馬力は大した事が無いですが今から52年前ですから、デザインと言いエンジンと言いやはり斬新で凄いと言えます。この三角窓の話に戻しますがトラックは別ですが、この時代の三角窓の素材はポルシェはアルミニウム製、ベンツやロールスロイスは真鍮製と錆に強い素材を使用していたにも関わらず、このフェアレディSR311はスチール製で錆に弱い素材を使用しております。今回はお客様より当社のメッキランク中メッキ加工(分厚いメッキ)をご希望されていますのでその加工方法をご紹介させて頂きたいと思います。中メッキ加工及び上メッキ加工のメッキ剥離にはクオリティを上げる為にシアンを用いて剥離致しますがろう漬け箇所はメッキと同じく溶けて無くなってしまうと言うデメリットが御座いますので写真にろう漬け箇所(黄色い)は溶けてしまう状態で剥離が完成致します。こうなる事から剥離終了後に板金加工を施さなければいけません。上メッキ加工にはアルミニウム製金属パテを使用致します。加工方法は以前の当社ブログで度々ご説明をさせて頂いておりますので今回は省略させて頂きますが大変な手間が掛ります。手間を掛けた下地修正から分厚くメッキを施していくのですが、最初にバフ磨きを施して素材の表面にあるピンホールや腐食痕が無くなる様に致します。この時、酷い腐食痕などは板金加工しなければ無くならない為に気になる場合はお客様にご連絡をさせて頂いた上で板金加工されるかされないかのご指示を仰ぎます。続いて銅メッキ加工を施して二回目のバフ研磨作業に於いて残りのピンホールを銅が削れた粉を用いて埋めていきます。そして二回目の銅メッキ加工を施します。この時にクロムメッキ加工の完成状態が分かります。更にニッケルメッキを分厚く施す事により錆びにくさが増します。通常、町のメッキ屋さんでは直ぐにニッケルメッキの槽からパーツを上げてしまう為に錆びやすい状態になっています。最後にクロムメッキ加工を施して完成品となります。この様な板金加工を施さなければいけない様な経年劣化部品でお困りのお客様はお電話してみて下さい。
カテゴリ:ブログ